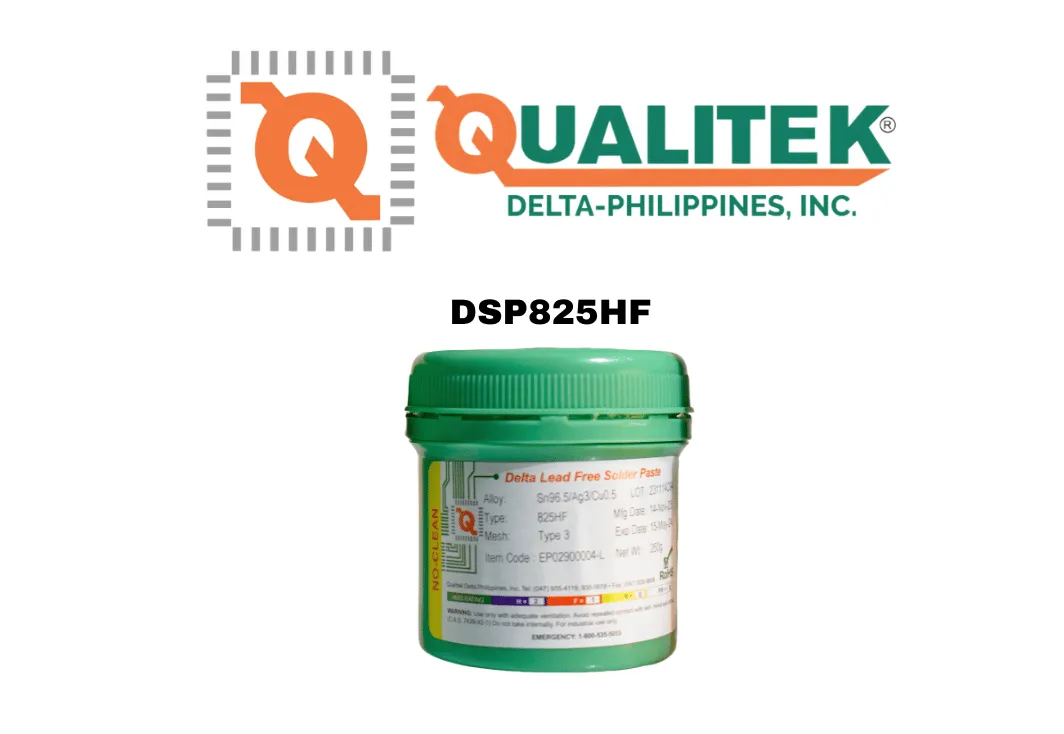
Solder Paste Perfection: Mastering Consistency for Flawless SMT Assembly
In the fast-paced world of Surface Mount Technology (SMT), consistency is the heartbeat of perfection. Achieving uniform solder paste application isn't just a technical necessity—it’s the foundation for flawless assembly, optimal yields, and long-term reliability of electronic products. Yet, even the most experienced SMT process engineers face challenges in maintaining this critical consistency. This article dives into proven techniques to master solder paste application, ensuring production quality that exceeds industry standards.
The Role of Solder Paste Consistency in SMT Assembly
Solder paste is more than just a bonding material; it’s the cornerstone of reliable SMT assembly. Uniform application ensures:
Accurate Component Placement: Prevents tombstoning and skewed components during reflow.
Strong Electrical Connections: Promotes reliable conductivity, minimizing defects.
Enhanced Process Yields: Reduces rework and scrap, saving time and costs.
Poor solder paste application can lead to catastrophic failures, from weak joints to complete board malfunction. As IPC standards emphasize, maintaining consistency in solder paste application is critical for ensuring reliable connections (IPC J-STD-005A).
Key Techniques for Uniform Solder Paste Application
1. Optimize Stencil Design
The stencil is the primary tool for depositing solder paste, and its design directly impacts application consistency. Consider these factors:
Aperture Size and Shape: Ensure apertures are properly sized to accommodate the component’s footprint while preventing under- or over-deposition.
Aspect Ratio and Area Ratio: Follow industry guidelines (IPC-7525A) to maintain optimal ratios, ensuring smooth paste release.
Material and Finish: Use high-quality, laser-cut stainless steel stencils with nanocoatings to reduce paste sticking and improve transfer efficiency.
2. Maintain Solder Paste Quality
The composition and handling of solder paste significantly affect its performance. Follow these best practices:
Storage and Shelf Life: Store paste at recommended temperatures (usually 0–10°C) to maintain viscosity and flux activity. Always check expiration dates.
Mixing and Thawing: Allow paste to thaw naturally to room temperature before use, ensuring homogeneous consistency without air bubbles.
Regular Inspection: Use rheometers to measure viscosity and confirm the paste meets manufacturing specs.
Enter DSP 825HF: A high-performance solder paste designed for consistency and reliability.
3. Fine-Tune Printing Parameters
Screen printing is the most common method for solder paste application, and precise control of the process is vital:
Squeegee Speed and Pressure: Maintain consistent pressure and speed to ensure even paste deposition without smearing or bridging.
Snap-Off Distance: Adjust the stencil-to-PCB distance for clean separation and accurate deposition.
Printing Environment: Control humidity and temperature to prevent paste drying or excessive moisture absorption.
4. Embrace Automation and Monitoring
Modern SMT lines benefit from advanced tools that ensure paste consistency:
Automatic Paste Dispensers: For precise and repeatable deposition, particularly on complex or high-mix boards.
Inline Inspection Systems: SPI (Solder Paste Inspection) tools monitor deposit volume, height, and shape in real-time, enabling immediate correction.
Why DSP 825HF is the Perfect Solution
DSP 825HF Solder Paste by Qualitek-Delta Philippines offers a game-changing solution for SMT perfection. Key features include:
Exceptional Printability: Achieves consistent, brick-like deposits, even for ultra-fine pitches as small as 0.3mm.
Enhanced Reflow Performance: Provides excellent wetting properties, ensuring void-free solder joints and smooth reflow profiles.
Halogen-Free, No-Clean Formulation: Meets stringent environmental standards, leaving benign residues that are compatible with conformal coatings.
Extended Stencil Life: Reduces downtime by maintaining paste performance over long production runs.
Multiple Alloy Options: Available in SAC305, LF217, and other alloys, tailored to your specific production needs.
Common Challenges and How DSP 825HF Solves Them
Clogged Stencil Apertures
Solution: DSP 825HF's smooth formulation ensures even flow and release, reducing stencil clogging.
Inconsistent Paste Deposition
Solution: With DSP 825HF’s optimized viscosity and tack properties, deposits remain consistent across runs.
Temperature-Induced Variations
Solution: The paste’s wide thermal stability ensures reliable performance, even in challenging environments.
The Impact of DSP 825HF on Production Quality
Studies by the Surface Mount Technology Association (SMTA) reveal that over 60% of SMT assembly defects originate from solder paste application issues. With DSP 825HF:
Reduce Defects: Minimize issues like insufficient solder, bridging, and tombstoning.
Enhance Reliability: Ensure strong solder joints capable of withstanding thermal and mechanical stress.
Boost Efficiency: Achieve higher throughput with less rework and scrap.
Final Thoughts
Solder paste perfection isn’t a luxury in SMT assembly—it’s a necessity. By focusing on stencil design, paste quality, printing parameters, and leveraging the advanced features of DSP 825HF, SMT process engineers can achieve the uniformity required for flawless assembly. Consistency in solder paste application sets the stage for high-quality electronics that perform reliably in the field.
Download the DSP 825HF Technical Data Sheet here to explore the full specifications.
Let us help you achieve solder paste perfection today!
References:
IPC J-STD-005A: Requirements for Soldering Pastes
IPC-7525A: Guidelines for Stencil Design
SMTA Proceedings: Advances in Solder Paste Technology
DSP 825HF Technical Data Sheet by Qualitek-Delta Philippines