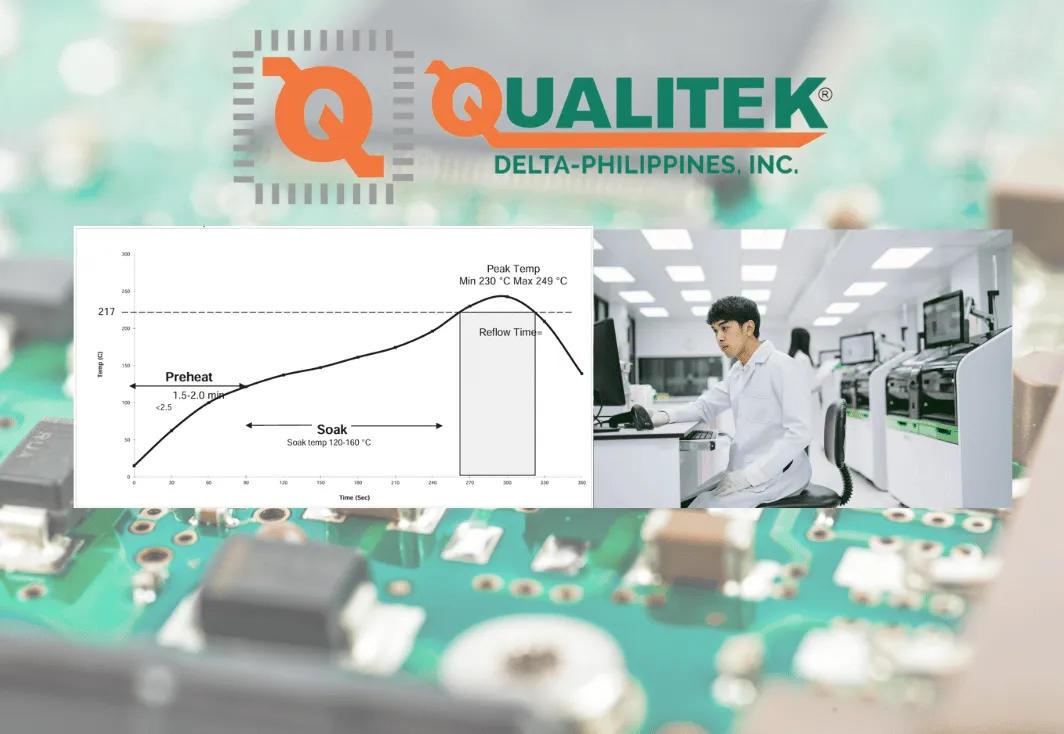
Reflow Right: Crafting Optimal Profiles for Perfect Solder Joints
Success in Surface Mount Technology (SMT) often comes down to mastering the details, and few details are as critical as the reflow profile. A poorly designed profile can turn the best solder paste into a reliability nightmare, leading to defects like voiding, bridging, or insufficient wetting. For SMT process engineers, crafting the perfect reflow profile is both an art and a science—one that ensures robust solder joints, minimal defects, and long-lasting performance.
This blog post delves into proven strategies for developing optimal reflow profiles, offering actionable insights to minimize defects and enhance joint reliability.
Why Reflow Profiling is Critical in SMT Assembly
Reflow soldering is the stage where the magic happens—solid solder paste transforms into liquid metal that forms reliable connections. But the process is fraught with challenges:
Temperature Sensitivity: Components and solder paste react differently to heat, and an imbalance can cause defects.
Defect Risks: Voiding, tombstoning, and incomplete wetting can all trace back to improper reflow profiles.
Long-Term Reliability: Improper profiles can lead to brittle joints or residual stresses, compromising product longevity.
According to IPC-7530 guidelines, reflow profile optimization is essential for achieving consistent soldering results and preventing assembly failures.
Key Elements of a Reflow Profile
To create an optimal reflow profile, you must understand its key stages:
Preheat Zone: Gradual heating reduces thermal shock and activates the flux in the solder paste.
Best Practice: Maintain a ramp rate of 0.5–2.0°C per second to avoid component stress.
Soak Zone: Allows even temperature distribution and flux activation.
Ideal Temperature: Hold at 140–160°C for 60–120 seconds to prepare solder paste for reflow.
Reflow Zone: The solder paste melts, forming metallurgical bonds.
Peak Temperature: Typically 20–40°C above the melting point of the solder alloy (e.g., 235–245°C for SAC305).
Cooling Zone: Rapid cooling solidifies the solder, forming strong joints.
Recommended Rate: 2–4°C per second to avoid brittle joints.
Common Defects and How to Prevent Them
1. Voiding
Cause: Outgassing during reflow or improper flux activation.
Solution: Use low-voiding solder pastes like DSP 825HF and ensure adequate soak time to allow flux volatiles to escape.
2. Tombstoning
Cause: Uneven heating of components during reflow.
Solution: Optimize ramp rates in the preheat zone and ensure uniform thermal distribution.
3. Insufficient Wetting
Cause: Low peak temperature or inadequate flux activity.
Solution: Increase the peak temperature within the alloy’s tolerance and use high-activity flux formulations.
Steps to Develop an Optimal Reflow Profile
1. Understand Your Solder Paste
Every solder paste has unique characteristics that influence its behavior during reflow. Check the technical data sheet (TDS) for:
Recommended Peak Temperature
Time Above Liquidus (TAL)
Optimal Heating Rates
Example: Qualitek’s DSP 825HF Solder Paste recommends a TAL of 60–90 seconds and a peak temperature of 240°C for best results.
2. Profile Your Oven
A well-calibrated reflow oven ensures consistent temperature across the PCB. Use thermocouples to monitor:
Component Surfaces
Board Edges and Center
Critical Solder Joints
3. Match the Profile to PCB Design
Consider factors like board thickness, component density, and thermal mass:
Dense Assemblies: Require slower ramp rates to ensure even heating.
Thin PCBs: Need careful cooling to prevent warping.
4. Monitor and Adjust
Use real-time monitoring tools to analyze your profile and make adjustments as needed. Software tools integrated with modern ovens can provide visual feedback and suggest corrections.
Why Qualitek-Delta Philippines is Your Partner in Reflow Perfection
At Qualitek-Delta Philippines, Inc., we understand the critical role of reflow profiling in SMT success. Our solder pastes, like the industry-leading DSP 825HF, are engineered to deliver consistent results under optimized profiles.
Key Benefits of DSP 825HF:
Low Voiding Properties: Reduces voiding even in challenging applications.
Wide Reflow Window: Adaptable to varying production conditions.
Halogen-Free Formulation: Ensures compliance with environmental regulations without sacrificing performance.
Pro Tips for Achieving Perfect Reflow
Calibrate Regularly: Ensure your oven maintains consistent temperatures by calibrating at least quarterly.
Use SPC (Statistical Process Control): Track key metrics like peak temperature and TAL to maintain process stability.
Leverage Supplier Support: Work with partners like Qualitek-Delta for expert guidance on solder paste behavior and profile tuning.
Final Thoughts: Reflowing Toward Perfection
Crafting the perfect reflow profile isn’t just a technical task—it’s a cornerstone of reliable SMT assembly. By understanding the nuances of solder paste behavior, leveraging advanced tools, and partnering with trusted suppliers like Qualitek-Delta Philippines, Inc. SMT process engineers can achieve flawless solder joints that stand the test of time.
Ready to Reflow Right?
Contact us today to learn how our soldering solutions and technical expertise can elevate your SMT processes.
Let’s perfect your reflow profile together.
References:
IPC-7530: Guidelines for Temperature Profiling for Mass Soldering
SMTA Proceedings: Advances in Reflow Soldering Technology
Qualitek-Delta Philippines Technical Data Sheets